PCB Shelf Life
- TapRen Team
- 4 days ago
- 6 min read
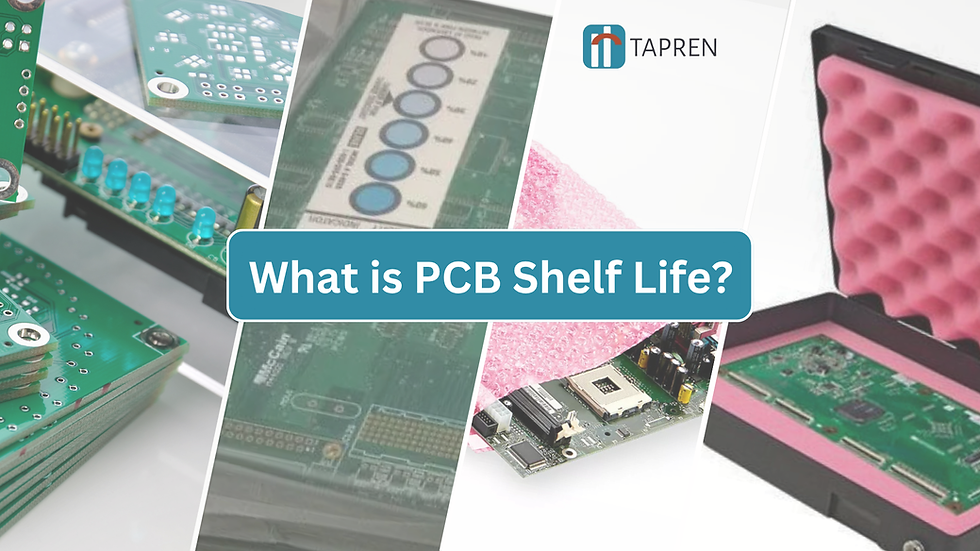
Introduction
This article focuses on designing PCBs that can withstand extreme conditions, such as high temperatures, moisture, and mechanical stress. It explores the materials, coatings, and design strategies that ensure reliability in harsh environments. You will learn about the key challenges faced in such designs and the innovative solutions that enhance the durability and performance of PCBs in demanding applications.
What is PCB Shelf Life?
The PCB shelf life is defined as the duration during which a Printed Circuit Board (PCB) remains capable of being stored under proper conditions without the degradation of quality or usability of the component.
During such time, the structural integrity, surface finish, and electrical properties of the PCB remain unchanged, thereby ensuring intended use performance. Upon reaching this point, the PCB faces issues associated with oxidation, delamination, or loss of conductivity, which affect its performance and reliability. Various factors related to storage conditions, material types, and handling practices define the proportion of the PCB's shelf life and the possibilities of its working.
Shelf life management ensures that the PCBs are in good condition, maintaining product standards with minimal risk of defects. This exercise is very relevant in ensuring that the life of electronics is long-lasting and reliable for consumers and industries.
Factors Affecting PCB Shelf Life

Everything plays a role in shelf life, from material selection to storage and handling practices; all of these factors are critical in maintaining performance and reliability over time.
The factors involved are material selection, storage conditions, surface finish, handling, and manufacturing quality.
Material Selection
The base material is one of the determining factors for the durability of PCBs. FR4, a standard glass-reinforced epoxy laminate, is typically stable but tends to deteriorate over time due to long-term exposure to humidity through hydrolysis. Polyimide-based boards offer significantly better resistance to water but at a higher cost. At the top level of performance, ceramic substrates show excellent thermal and environmental stability.
The use of materials as suggested by IPC-4101, ensures the extended PCB shelf life.
Storage Conditions
Temperature and humidity have a significant impact on the longevity of PCBs. High humidity accelerates copper oxidation via the reaction:
4Cu + O₂ + 2H₂O → 4Cu(OH)₂, compromising conductivity.
IPC-1601 recommends storing PCBs at 15–30°C and below 50% relative humidity, utilizing moisture barrier bags and desiccants to mitigate environmental effects.
Surface Finish
The selection of surface finish affects shelf life.
ENIG resists oxidation but can experience "black pad" defects if the process is not properly controlled. Besides, the nickel layer of ENIG further prevents copper diffusion.
OSP must be stored in nitrogen-sealed bags to perform in humid atmospheres. The OSP coating degree rapidly reduces, which affects solderability over time. HASL is inexpensive but does tarnish. It has a better shelf life than OSP and others.
The surface finish selection should align with IPC-4552 and IPC-6012 to ensure the durability of the PCB.
Handling Practices
Poor handling introduces oils and contaminants that speed up corrosion. IPC-A-600 advocates for clean handling, which includes the use of gloves and antistatic tools. Mechanical stress is also to be avoided to prevent micro-cracks that can worsen with thermal cycling.
Manufacturing Quality
Poor manufacturing can undermine the longevity of a PCB. Poor lamination results in delamination, while plating defects expose copper to corrosion. Misaligned vias increase resistance and weaken connections. Adherence to IPC-6012 guidelines will ensure structural integrity and performance reliability.
By optimizing these factors, the shelf life of PCBs can be extended, ensuring reliability in electronic applications.
Best Practices for Extending PCB Shelf Life

The best practices of storing and handling PCBs can only be maintained if their quality is to be preserved for an extended shelf life, ensuring they are available when required.
Store in a Controlled Environment:
The storage conditions for the PCBs are crucial and should be maintained in a cool, dry area with low humidity. Ideal storage conditions include temperatures between 20 °C and 25°C and humidity below 50%.
Use Proper Packaging
Proper packaging prevents the PCBs from environmental exposure. Anti-static bags and packaging, sealed by vacuum, limit exposure to moisture and air, thereby protecting against oxidation and other contaminants that can cause electrostatic discharge damage.
Carefulness and Sensitivity
Poor handling introduces numerous contaminants that degrade PCBs. Always use gloves or tweezers and avoid direct contact, as oils and dirt from your hands can lead to oxidation. Handle PCBs gently to prevent physical damage, such as scratches or bending.
Rotate Stock
The implementation of the FIFO system would ensure that older PCBs are dealt with first. This practice prevents the pointless aging of products in storage, hence reducing the risk of any batch exceeding its recommended shelf life.
Industry Standards and Guidelines
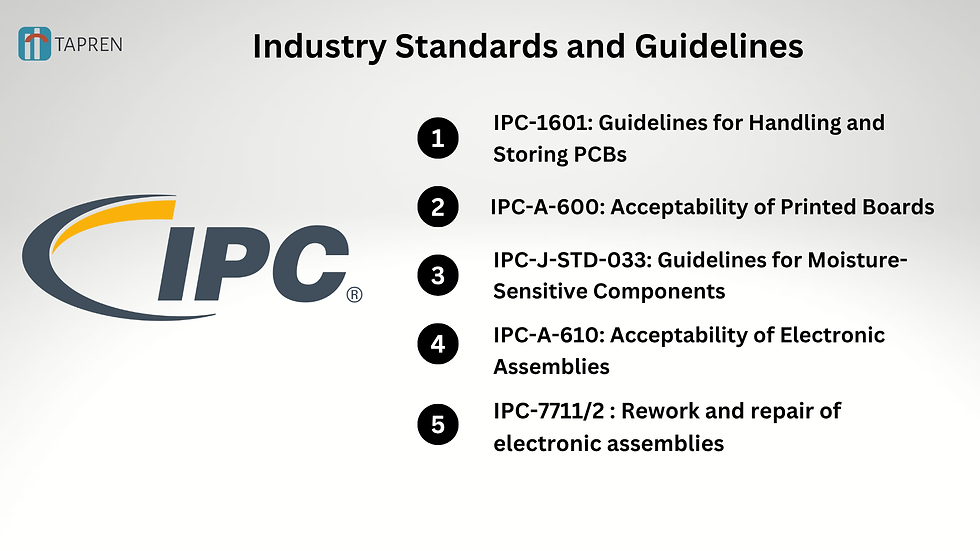
Industry specifications, such as those from the IPC or Association Connecting Electronics Industries, require handling, storage, and inspection according to a set standard. Conformance to these basic standards ensures consistent quality over an extended period and reliable field performance.
IPC-1601: Guidelines for the Handling and Storage of Printed Boards
This standard addresses the handling and storage of PCBs to prevent damage due to environmental factors, including humidity, temperature, and contaminants. The standard outlines the optimal packaging and storage conditions, as well as the use of moisture barrier bags, to ensure the best preservation of the PCBs.
IPC-A-600: Acceptability of Printed Boards
This document presents visual acceptability criteria for printed boards, covering topics such as surface quality, plating, and solderability. It is vital in trying to locate defects that could affect a PCB's shelf life or operational expectations.
IPC-J-STD-033: Handling, Packing, Shipping, and Use of Moisture/Reflow Sensitive Components
This document outlines the requirements applicable to moisture-sensitive devices, including PCBs with finishes or other materials, packaging requirements, humidity control, and baking procedures to remove moisture before reflow soldering.
IPC-A-610: Acceptability of Electronic Assemblies
While targeting assembled boards, this document details PCB handling considerations related to quality, either in an assembled state or before or after assembly. Cleanliness, storage, and adherence to best inspection practices all contribute to continued reliability.
IPC-7711/2: Rework and repair of electronic assemblies
This document covers rework and repair techniques that do not compromise the integrity or lifespan of the PCBs. It provides detailed instructions on how damaged or defective boards should be treated and processed.
By following this IPC standard on rework and repair, manufacturers and users can ensure the production of high-quality, durable, reliable, and safe PCBs for their intended applications.
Signs of PCB Shelf Life Expiration
Recognizing the signs of PCB shelf life expiration is vital to avoiding degraded boards that compromise electronics performance and safety.
Oxidation or Discoloration
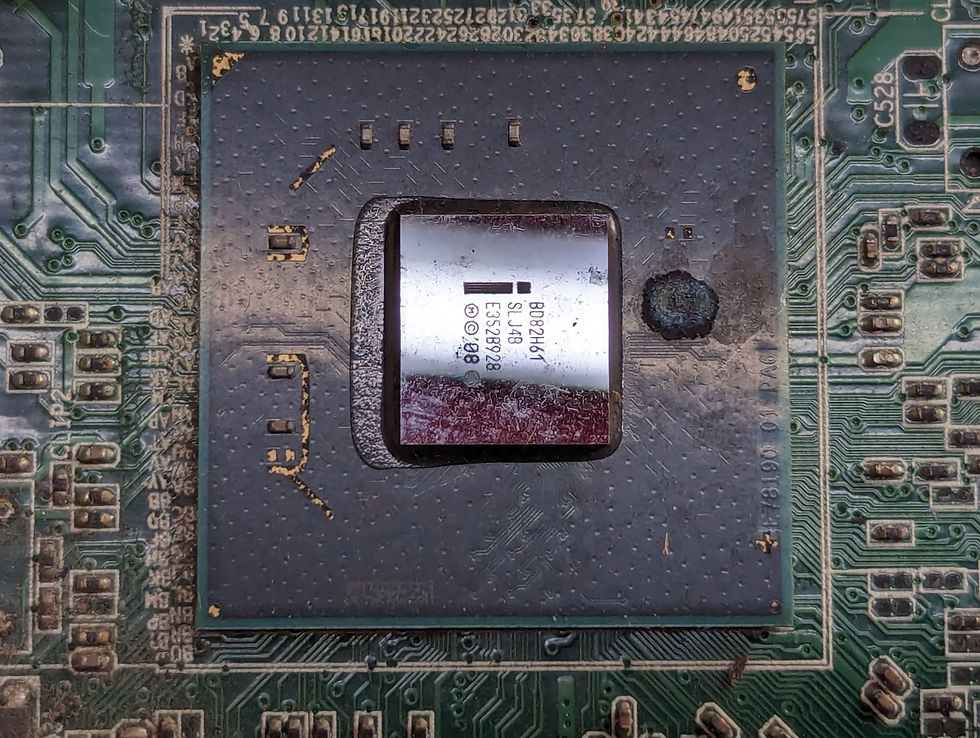
One other fairly obvious indication of shelf life expiry is oxidation or discoloration on the surface of the PCB. It typically appears as tarnish, dark spotting, or corrosion on exposed copper or solder pads. This may affect solderability and electrical conductivity, therefore affecting functionality.
Peeling or Delamination

If the layers in the PCB begin separating, that becomes a sure indicator of material degradation. Delamination typically occurs due to excessive exposure to humidity, high temperatures, or inadequate storage conditions. This can even affect the overall structural integrity and disturb the electrical pathways inside the PCB.
Loss of Functionality

The failures of electrical properties in expired PCBs may be due to broken connections, increased resistance, or short circuits. That is because, in the long run, a compromised material, oxidation, or physical damage will make the board unreliable or even completely non-functional in devices.
Early identification of these signs by both manufacturers and users can help them avoid expensive failures while ensuring the continued reliability of their electronic products.
Common Mistakes That Impact PCB Shelf Life

The quality and shelf life of PCBs depend on how well one can avoid the common mistakes in handling and storing them.
Poor Storage Conditions
Storing the PCBs in highly humid conditions or at extremely high or low temperatures will cause oxidation, warping, and a reduction in shelf life. Store always in controlled conditions.
Inspection Negligence
Missed routine inspections may lead to defects such as corrosion and delamination, which can go undetected and result in faulty performance. Pre-use checks are absolutely necessary.
Poor Handling
Handling without gloves and with inappropriate tools may introduce oxidation and damage to the PCB due to oils and contaminants. Always take care and take protective measures when handling.
Conclusion
In all, shelf life management of a PCB is crucial in maintaining the long-term reliability of electronic devices and optimizing their performance. This prevents the degradation of PCBs under proper storage conditions, with appropriate packaging, and adherence to best practices for handling. With proactive care, it is possible to extend the life of PCBs, prevent failures, and maintain the high quality of electronic products.
Key Takeaway
Management of PCB shelf life is of paramount importance for the reliability and longevity of electronic devices. Proper storage conditions, including controlled temperature and humidity, combined with careful handling and packaging, can significantly extend the life of a PCB. Regular inspection and adherence to industry standards allow early identification of potential defects that may lead to malfunctioning. By observing best practices and rotating stock, PCBs can be preserved effectively. This proactive management of the PCB's shelf life minimizes the risk of failure, ensuring the availability of high-quality and safe electronic equipment in service.
Next Read:
Zero PCB: Mastering Permanent Prototyping
Comments